Have a Question?
Find Your Answer Here.
Explore our comprehensive FAQs to find detailed answers regarding our services. If you have additional inquiries, please feel free to contact us directly for personalized assistance.
Explore Our Knowledge Base
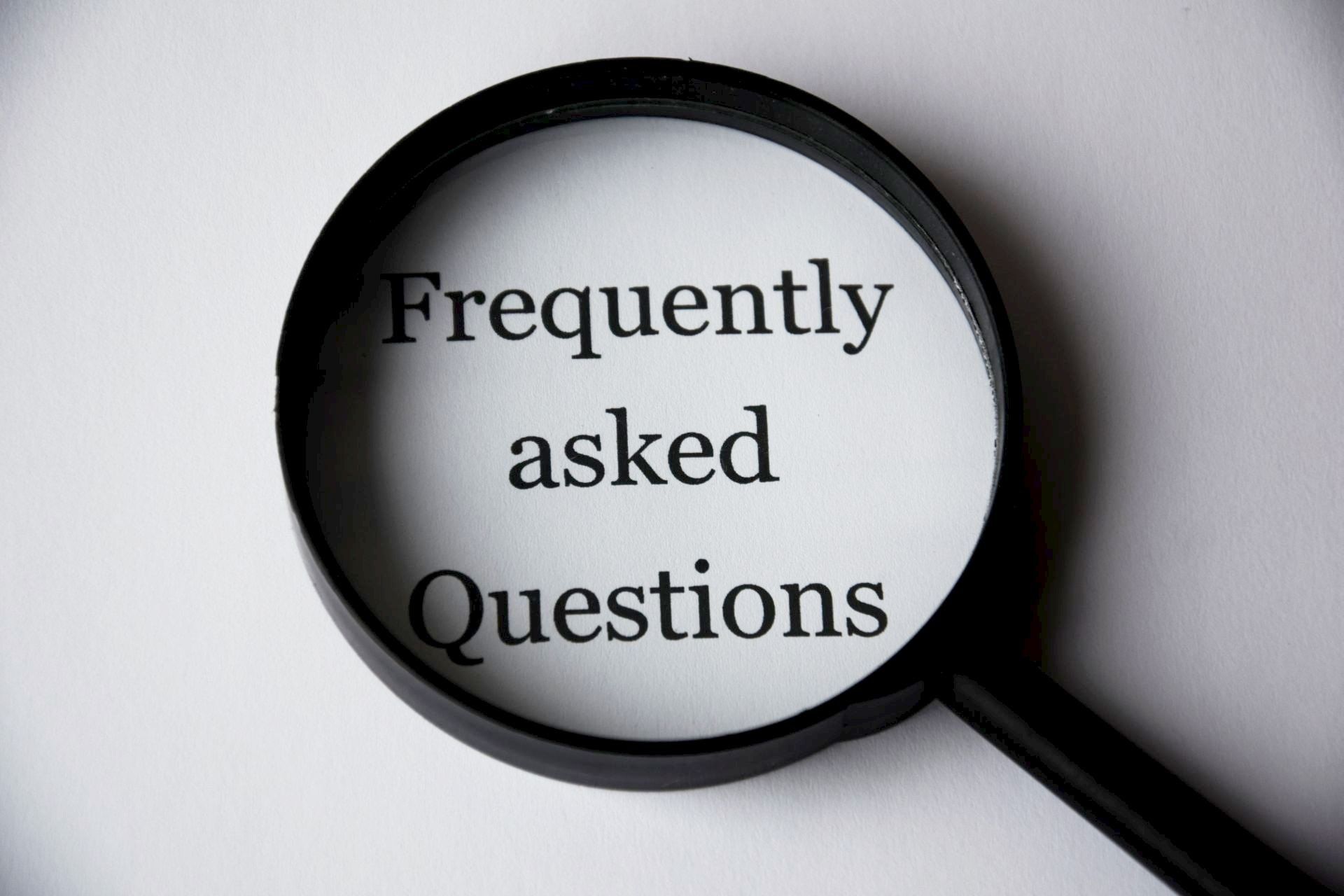
What are your business hours?
Our business hours are Monday – Friday, 9:00 AM – 5:00 PM (PST). We are closed on weekends and major holidays.
What is your turnaround time?
Our standard turnaround time is 3 to 5 business days, depending on job complexity, quantity, and current production queue. However, we offer expedited processing for urgent requests, including 48-hour, 24-hour, and even same-day service. For local customers, some jobs can even be completed while you wait in our lobby. Expedited services involve premium charges and are subject to availability. Please contact us with your specific requirements, and we’ll work to meet your deadlines.
What if my material isn’t listed?
Our material list covers a broad range of substrates, but it may not include everything we can process. If your material isn’t listed, contact us—there’s a good chance we can work with it. Our team is experienced in handling a variety of hard and brittle materials, and we’re always open to discussing your specific requirements.
Can I drop the wafer off at your facility?
Absolutely, clients are welcome to drop off wafers at our facility during designated business hours. Kindly coordinate with our team to ensure seamless reception.
Can I watch you dice my wafer?
Certainly! You are more than welcome to observe the dicing process. We believe in fostering transparency and trust with our clients, and we're happy to accommodate your interest in witnessing our meticulous work firsthand. Please let us know your preferences, and we'll make the necessary arrangements for your visit.
What accuracy can you maintain?
With our cutting-edge equipment, we consistently achieve precision down to the micron level, ensuring that we meet the exacting standards of our clients. Typically, we maintain an impressive accuracy of +/- 10 microns, showcasing our commitment to delivering top-notch results.
What wafer sizes can APD handle?
APD can handle a wide range of wafer sizes, up to 300 mm in diameter.
What is the thinnest cut you can make?
APD can make cuts as thin as 20 microns wide with high precision.
What is the thinnest wafer you can process?
We can process wafers as thin as 50 microns.
What is the thickest wafer you can cut?
We have successfully cut wafers up to 10 mm thick in the past, but this is not our limit. If you have thicker wafers, we may be able to accommodate your request depending on the material and requirements. Please provide details, and we’ll assess feasibility
Can you perform trenching with variable depths?
Yes, APD can perform trenching with variations in depths of less than 5 micrometers over a 300-millimeter cut.
Does Dicing Always Require Photoresist for Protection?
While not always mandatory, the use of photoresist is strongly recommended for optimal protection during the dicing process, particularly for delicate materials or when stringent cleanliness standards must be upheld.
When is Photoresist Recommended for Dicing?
Photoresist is advised for dicing applications where the material's integrity and cleanliness are paramount concerns, ensuring a protective layer against potential damage or contamination during the precision cutting process.
How do you measure chipping?
Chipping is measured using a calibrated microscope. Viewing the topside of the part, find the largest chip along the edge of the kerf. Measure the distance from the edge of the kerf to the top of the chip. Backside chipping is measured the same way, but the part has to be removed from the holding medium and flipped over to expose the backside.
What does it cost to dice a wafer?
Our pricing structure is tailored to the individual requirements of each project, accounting for factors such as wafer size, material composition, and specific service needs. Please reach out to us for a personalized quote.
Do I have to pay in advance?
Our payment terms are flexible and tailored to suit the specifics of each project. Please feel free to discuss your payment preferences with us, and we'll ensure a mutually agreeable arrangement. Typically, payment is required upon the completion of the project and before shipping. We're committed to ensuring transparency and clarity in all our transactions.
Do you accept credit cards?
Absolutely, we're pleased to offer the convenience of credit card payments, alongside ACH payments, to ensure a seamless experience for our valued clients.
Do we give discounts to Universities?
Unfortunately, we currently do not offer discounts specifically tailored to universities.